Introduction
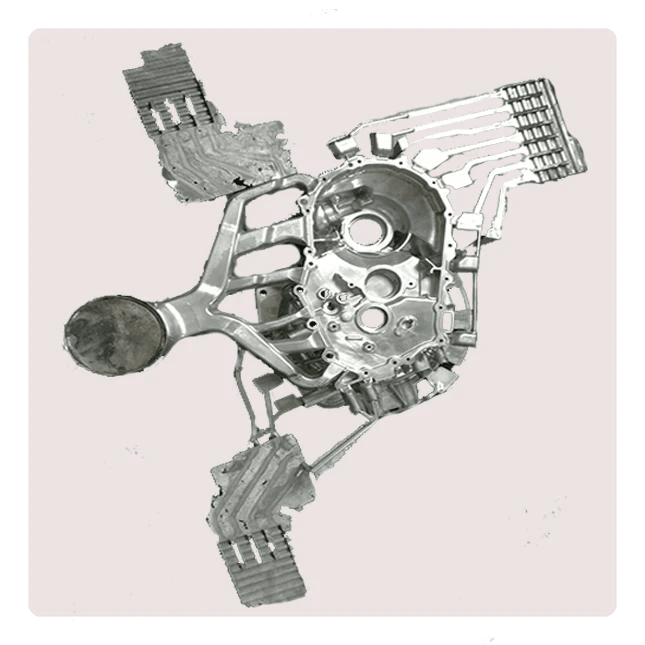
Welcome to the fascinating world of high pressure casting, a revolutionary method in metal casting that has transformed the manufacturing industry. High pressure casting, also known as die casting, is a process that involves injecting molten metal into a steel mold under high pressure. This results in precise and complex shapes with excellent surface finishes, making it an ideal choice for a wide range of applications.
Understanding High Pressure Casting
High pressure casting, or die casting, is a manufacturing process that utilizes high pressure to force molten metal into a mold cavity. The mold is typically made from steel and is designed to produce intricate and detailed parts with high accuracy and consistency. This method allows for the production of complex shapes that are difficult or impossible to achieve with other casting methods.
Benefits of High Pressure Casting
The benefits of high pressure casting are numerous and significant. This method offers fast production rates, tight tolerances, excellent surface finishes, and the ability to produce thin-walled parts with intricate details. Additionally, die casting dies have a long lifespan and can produce thousands of parts before needing replacement, making it a cost-effective solution for mass production.
Applications of High Pressure Casting
High pressure casting is widely used in various industries due to its versatility and efficiency. It is commonly used for producing automotive parts such as engine components and transmission housings, as well as consumer electronics like smartphone cases and laptop enclosures. The precision and durability of die cast parts also make them suitable for aerospace components and medical devices.
The Basics of High Pressure Casting
High pressure casting is a metal casting process that uses high pressure to force molten metal into a mold cavity. This process is commonly used for manufacturing complex shapes with thin walls and excellent surface finish.
What is High Pressure Casting?
High pressure casting, also known as die casting, is a process where molten metal is injected into a steel mold at high pressure. The mold cavity is created using two hardened tool steel dies which have been machined into shape and work similarly to an injection mold during the process.
The Process of High Pressure Casting
The process of high pressure casting begins with the preparation of the die casting machine, which includes clamping the two die halves together and injecting the molten metal into the cavity at high speeds and pressures. Once the metal has solidified, the dies are opened and the casting ejected.
Advantages of High Pressure Casting
One of the main advantages of high pressure casting is its ability to produce parts with tight tolerances and excellent surface finish. Additionally, this method allows for fast production rates and can produce parts with thin walls, reducing material usage and weight.
By understanding the basics of high pressure casting, including what it entails, how it works, and its advantages, manufacturers can make informed decisions about utilizing this efficient manufacturing method for their production needs.
Materials Used in High Pressure Casting
Aluminum Casting in High Pressure Casting
Aluminum casting is a popular choice for high pressure casting due to its lightweight and corrosion-resistant properties. The metal is melted and injected into the die cast dies at high pressure, resulting in precise and detailed parts. Buttler Precision Machinery Co., Ltd. offers cutting-edge technology for aluminum casting, ensuring high-quality and durable components for various industries.
Furthermore, aluminum casting offers excellent thermal conductivity, making it an ideal choice for parts that require heat dissipation. This property ensures that components can withstand high temperatures without compromising performance, making them suitable for a wide range of applications in the automotive, aerospace, and electronics industries. With Buttler Precision Machinery Co., Ltd.'s advanced technology and expertise in aluminum casting, customers can expect reliable and efficient solutions for their specific needs.
Zinc Casting in High Pressure Casting
Zinc casting is another key material used in high pressure casting, known for its excellent dimensional stability and thin wall capabilities. This makes it suitable for intricate designs and complex shapes, ideal for automotive and electronic components. With Ningbo Buttler Precision Machinery Co., Ltd.'s expertise in zinc casting, you can expect top-notch quality and precision in every part produced.
Furthermore, zinc casting offers excellent corrosion resistance, making it a durable and long-lasting material for various applications. With Ningbo Buttler Precision Machinery Co., Ltd.'s advanced technology and state-of-the-art equipment, we can ensure that every zinc casting meets the highest standards of quality and performance. Whether it's for automotive parts or electronic components, you can rely on our expertise to deliver superior zinc castings that exceed your expectations.
Die Casting Dies for High Pressure Casting
Die casting dies play a crucial role in the high pressure casting process, as they are used to create the mold cavity into which the molten metal is injected. Buttler Precision Machinery Co., Ltd.'s innovative tooling designs are engineered to maximize performance and casting quality while minimizing the need for secondary operations. Their Engineering Design Review Process ensures cost-effective manufacturing without compromising on part design or quality.
In addition to their innovative tooling designs, Buttler Precision Machinery Co., Ltd. also offers customization options for die casting dies to meet the specific needs of each project. By working closely with clients, they are able to tailor the mold cavity and overall die design to ensure optimal performance and casting quality. This level of flexibility sets them apart from other manufacturers and allows for a truly customized high pressure casting solution.
Unique Features of High Pressure Casting
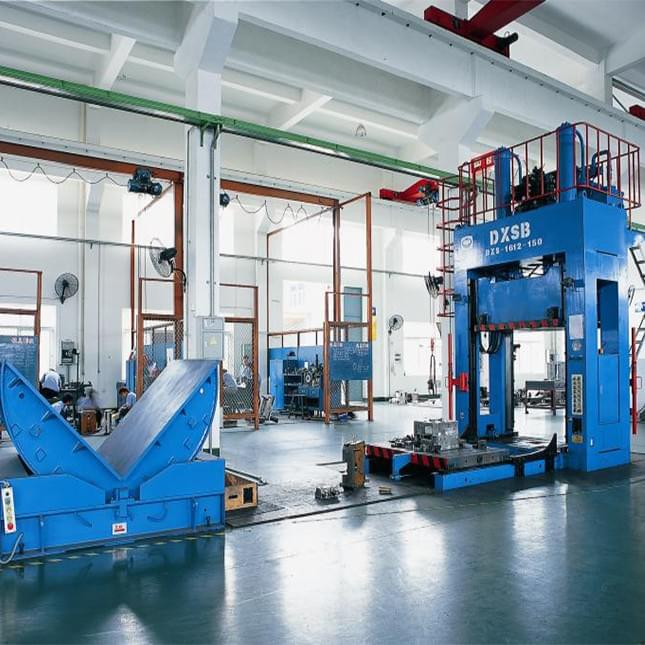
Precision in High Pressure Casting
High pressure casting offers exceptional precision in the production of metal castings, ensuring that the final products meet tight tolerances and exact specifications. This level of precision is achieved through the use of advanced die casting dies and state-of-the-art machinery, resulting in high-quality parts that require minimal post-processing.
Surface Treatment in High Pressure Casting
Surface treatment is a crucial aspect of high pressure casting, as it enhances the appearance and functionality of the casted parts. Ningbo Buttler Precision Machinery Co., Ltd. specializes in providing a wide range of surface treatment options, including powder coating, anodizing, and painting, to ensure that the finished products meet the highest standards of quality and durability.
Smart Part Engineering for High Pressure Casting
Ningbo Buttler Precision Machinery Co., Ltd.'s smart part engineering approach involves utilizing innovative tooling designs to optimize part designs for cost-effective manufacturing. By leveraging their Engineering Design Review Process, they are able to maximize performance and casting quality while minimizing the need for secondary operations, resulting in superior diecast parts.
Applications of High Pressure Casting
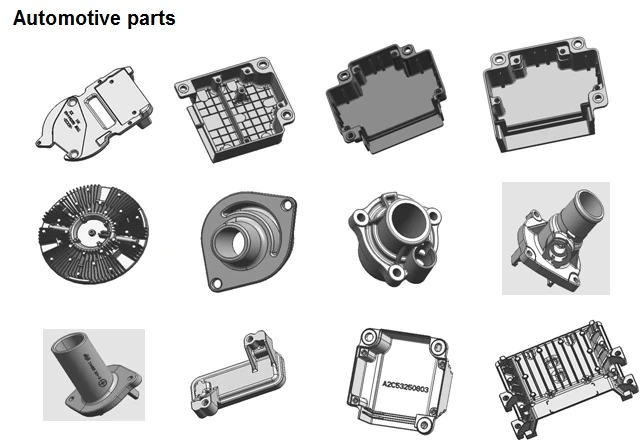
High pressure casting is widely used in various industries due to its ability to produce complex and high-quality metal castings. One popular application of high pressure casting is in the manufacturing of outdoor lamp series, where intricate designs and precise dimensions are crucial. Companies like Buttler Precision Machinery Co., Ltd. specialize in providing die-casting molds and aluminum castings for outdoor lighting fixtures, ensuring durability and aesthetic appeal.
Outdoor Lamp Series in High Pressure Casting
The process of high pressure casting allows for the creation of intricate and detailed designs, making it ideal for producing outdoor lamp series that require both functionality and visual appeal. With the use of die casting dies specifically engineered for high pressure casting, companies like Buttler can achieve consistent quality and precision in their aluminum castings for outdoor lighting applications.
Automotive Parts in High Pressure Casting
In the automotive industry, high pressure casting is utilized to manufacture various parts such as engine components, transmission housings, and structural elements. The use of diecast dies designed for high pressure casting ensures that automotive parts meet stringent performance and safety requirements while maintaining cost-effectiveness. Buttler Precision Machinery Co., Ltd.'s expertise in aluminum and zinc castings makes them a reliable partner for automotive part production.
Gas Appliance Parts in High Pressure Casting
Gas appliances require durable and heat-resistant components, making high pressure casting an ideal manufacturing method for producing parts such as burner heads, valve bodies, and heat exchangers. With the expertise of companies like Buttler Precision Machinery Co., Ltd., gas appliance manufacturers can benefit from precision-engineered die casting dies that enhance the quality and performance of their cast components.
By leveraging the capabilities of high pressure casting across these diverse applications, industries can achieve superior quality metal castings that meet their specific requirements while optimizing production efficiency.
Advancements in High Pressure Casting
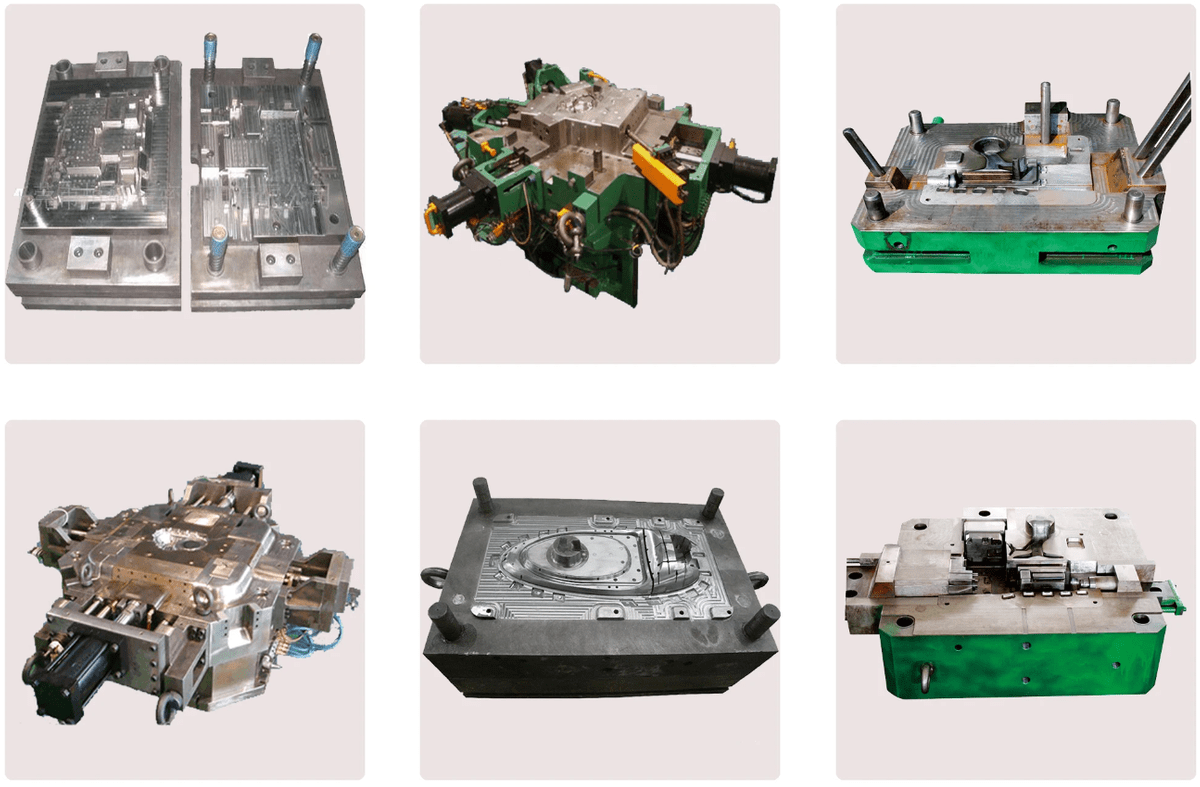
As high pressure casting continues to evolve, there have been significant innovations in die casting molds. Buttler Precision Machinery Co., Ltd. is at the forefront of this advancement, offering state-of-the-art die casting dies that are designed for maximum efficiency and quality. These innovative molds are engineered to optimize the casting process, resulting in superior metal castings with minimal defects and high precision.
Innovations in Die Casting Molds
Buttler Precision Machinery Co., Ltd. has revolutionized the die casting industry with their cutting-edge die casting dies. These molds are meticulously designed to enhance the high pressure casting process, ensuring that each part is produced with exceptional accuracy and consistency. By leveraging advanced technology and engineering expertise, Buttler has set a new standard for die cast tooling, delivering unparalleled performance and reliability.
Furthermore, Buttler's die casting molds are designed to withstand the high pressures and temperatures involved in the casting process, ensuring durability and longevity. This means that manufacturers can rely on these molds to consistently produce high-quality parts without the need for frequent replacements or repairs. As a result, production costs are reduced, and overall efficiency is improved, making Buttler's molds a cost-effective solution for die casting needs.
Evolution of High Pressure Casting Technology
The evolution of high pressure casting technology has been driven by the demand for more efficient and cost-effective manufacturing processes. With advancements in automation, robotics, and digitalization, high pressure casting has become increasingly sophisticated and streamlined. Buttler Precision Machinery Co., Ltd. has embraced these technological advancements to elevate their capabilities in producing top-quality aluminum castings and zinc castings that meet the rigorous standards of modern industries.
As high pressure casting technology continues to evolve, the industry is seeing a shift towards the use of sustainable materials and processes. With a growing emphasis on environmental responsibility, manufacturers like Buttler Precision Machinery Co., Ltd. are investing in research and development to explore alternative materials and energy-efficient production methods. This focus on sustainability not only aligns with global trends but also positions companies for long-term success in an increasingly eco-conscious market.
Future of High Pressure Casting
Looking ahead, the future of high pressure casting holds tremendous promise for continued innovation and growth. As industries continue to demand higher performance parts with complex designs, the need for advanced high pressure casting technology will only intensify. Buttler is poised to lead this charge by investing in research and development to push the boundaries of what is possible in metal casting, ensuring that they remain at the forefront of the industry.
As industries continue to evolve, the demand for high pressure casting technology will only increase. This presents an exciting opportunity for Buttler to develop cutting-edge solutions that meet the ever-changing needs of their clients. By staying ahead of the curve and continuously innovating, Buttler can solidify their position as a leader in the high pressure casting industry.
Conclusion
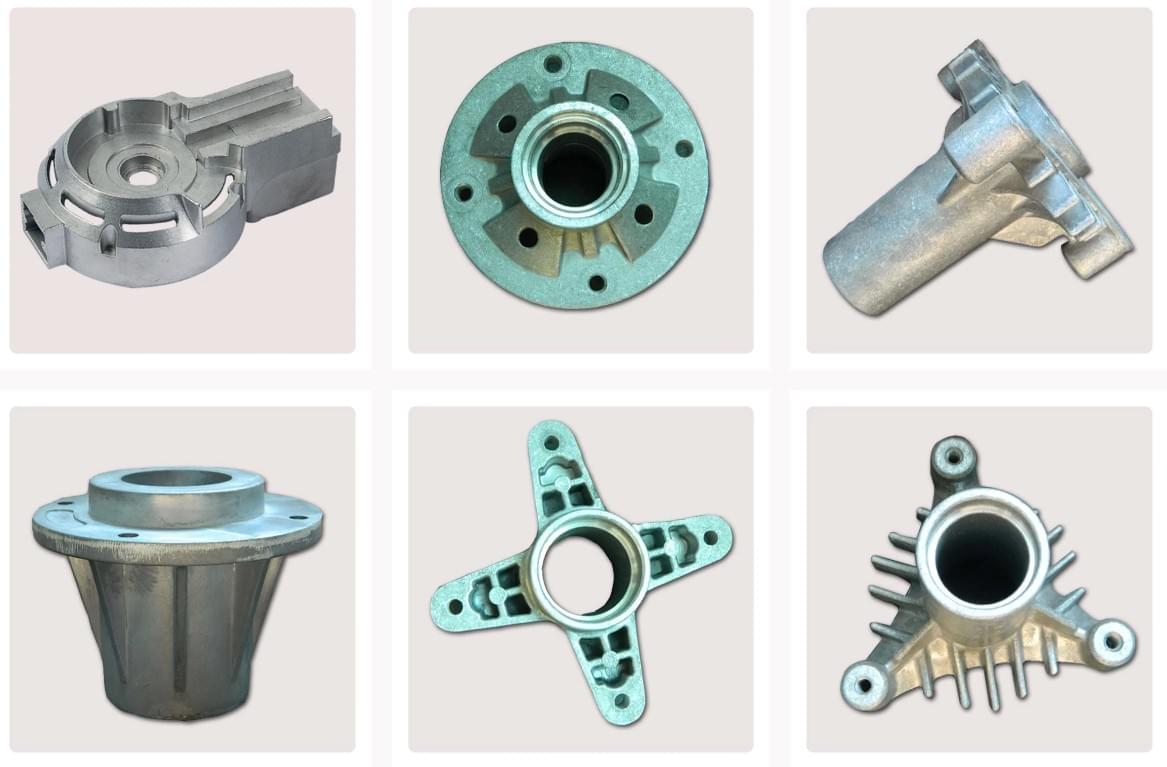
High pressure casting offers numerous sustainability benefits, including reduced material waste, energy efficiency, and the ability to recycle scrap metal. By choosing high pressure casting, manufacturers can minimize their environmental impact and contribute to a more sustainable future.
Sustainability Benefits of High Pressure Casting
With high pressure casting, manufacturers can significantly reduce material waste by utilizing precise die casting molds and smart part engineering to produce accurate and high-quality metal castings. This process also requires less energy compared to other manufacturing methods, contributing to overall energy efficiency. Additionally, the ability to recycle scrap metal in high pressure casting further enhances its sustainability benefits.
Industry Impact of High Pressure Casting
The impact of high pressure casting on various industries is substantial, as it provides cost-effective solutions for producing complex metal parts with exceptional precision and surface quality. From automotive components to gas appliance parts, the versatility of high pressure casting has revolutionized the manufacturing sector by offering efficient and reliable production methods for a wide range of applications.
Choosing the Right High Pressure Casting Partner
When selecting a high pressure casting partner, it is crucial to consider factors such as expertise in die-casting molds, aluminum and zinc castings, surface treatment capabilities, and smart part engineering solutions. Ningbo Buttler Precision Machinery Co., Ltd., for example, specializes in providing innovative tooling designs engineered for cost-effective manufacturing while maximizing performance and minimizing the need for secondary operations.