Introduction
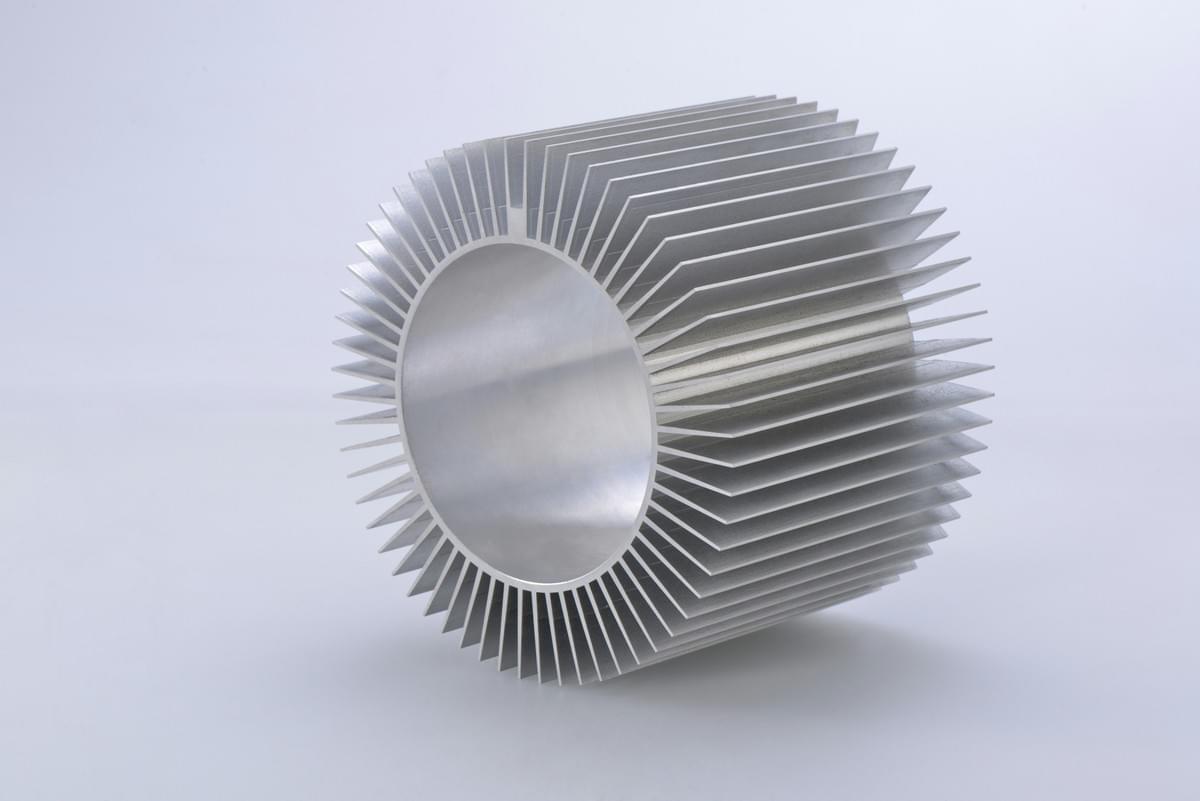
When it comes to manufacturing, the versatility of aluminum casting alloys is unmatched. These alloys offer a wide range of properties, making them suitable for various applications across different industries. Understanding the most used cast aluminum alloys and why they matter is crucial for making informed decisions in product design and manufacturing.
The Versatility of Aluminum Casting Alloys
Cast aluminum alloys are known for their lightweight yet durable nature, making them ideal for a variety of products. Their high strength-to-weight ratio allows for the creation of sturdy components without adding unnecessary bulk.
Understanding the Most Used Alloys
The cast aluminum alloys list includes popular options such as 6061, 356, and 380, each with its own unique properties and benefits. These alloys are carefully engineered to meet specific requirements in terms of strength, corrosion resistance, and thermal conductivity.
Why Aluminum Casting Alloys Matter
The choice of casting aluminum alloy can significantly impact the performance and longevity of a product. Whether it's for automotive parts, outdoor lighting fixtures, or gas appliance components, selecting the right alloy is crucial to ensure optimal functionality and durability.
Benefits of Aluminum Casting Alloys
When it comes to cast aluminum alloys, the benefits are numerous and impressive. Firstly, these alloys are lightweight and durable, making them ideal for a wide range of applications. Whether it's automotive parts or outdoor lighting fixtures, the lightweight nature of cast aluminum alloys ensures ease of handling and installation.
Lightweight and Durable
Cast aluminum alloys are known for their exceptional strength-to-weight ratio, making them a popular choice in industries where weight is a critical factor. This combination of lightweight properties and durability makes cast aluminum alloys suitable for various applications, from aerospace components to consumer electronics.
High Corrosion Resistance
Another key benefit of cast aluminum alloys is their high corrosion resistance. This makes them an excellent choice for outdoor applications where exposure to moisture and harsh weather conditions is inevitable. From marine equipment to architectural elements, the ability of cast aluminum alloys to withstand corrosion makes them a reliable material choice.
In addition to their high corrosion resistance, cast aluminum alloys also offer excellent thermal conductivity. This means that they are able to efficiently transfer heat, making them ideal for applications where heat dissipation is important. Whether used in automotive components or electronic devices, the exceptional thermal conductivity of cast aluminum alloys ensures optimal performance and reliability.
Excellent Thermal Conductivity
In addition to being lightweight and corrosion-resistant, cast aluminum alloys also boast excellent thermal conductivity. This property is particularly valuable in applications where efficient heat dissipation is crucial, such as in heat sinks for electronic devices or industrial machinery components.
Furthermore, the high thermal conductivity of cast aluminum alloys also makes them ideal for use in automotive components such as engine cylinder heads and brake calipers. The ability to efficiently transfer heat away from critical engine and braking systems helps improve overall performance and reliability. This makes cast aluminum alloys a popular choice among automotive manufacturers looking to enhance the durability and efficiency of their vehicles.
Commonly Used Aluminum Casting Alloys
When it comes to cast aluminum alloys, there are several popular options that are widely used in various industries. These alloys are known for their excellent properties and versatility, making them ideal for a wide range of applications.
6061 Aluminum Alloy
6061 aluminum alloy is also known for its versatility, making it a popular choice for a wide range of applications. Its ability to be easily machined, welded, and formed allows for greater design flexibility and customization. This makes it an ideal option for manufacturers looking to create complex and intricate components with ease. Additionally, its resistance to stress cracking further enhances its suitability for demanding environments, ensuring long-lasting performance in various industrial settings.
356 Aluminum Alloy
356 aluminum alloy is another popular choice for casting applications, known for its good fluidity and excellent castability. This alloy is commonly used in automotive parts, engine components, and general engineering applications due to its high strength and good corrosion resistance.
In addition to its mechanical properties, 356 aluminum alloy also offers good thermal conductivity, making it an ideal choice for heat exchangers and other applications where efficient heat transfer is crucial. This alloy is also highly machinable, allowing for intricate designs and precise finishing. Its versatility and durability make it a top choice for manufacturers looking to produce high-quality, long-lasting components.
380 Aluminum Alloy
380 aluminum alloy is widely utilized in die casting processes due to its exceptional fluidity and ease of casting. It offers good mechanical properties and is often used in the production of intricate components such as pump housings, valve bodies, and electrical connectors.
Additionally, 380 aluminum alloy is known for its excellent corrosion resistance, making it an ideal choice for components exposed to harsh environmental conditions. This alloy also exhibits good thermal conductivity, which is crucial for applications requiring heat dissipation. Its combination of strength and lightweight properties makes it a versatile material for a wide range of industrial and consumer products.
By understanding the unique properties of each commonly used cast aluminum alloy, manufacturers can make informed decisions when selecting the best material for their specific application needs.
Applications of Cast Aluminum Alloys
Automotive Industry
One of the most common applications for cast aluminum alloys is in the automotive industry. These alloys are used to manufacture engine components, transmission cases, and structural parts due to their lightweight and durable nature. The high corrosion resistance of cast aluminum alloys also makes them ideal for use in vehicle parts that are exposed to harsh environmental conditions.
In addition to vehicle parts, cast aluminum alloys are also widely used in outdoor lighting fixtures. The lightweight and corrosion-resistant properties of these alloys make them an ideal choice for outdoor applications where the fixtures are exposed to varying weather conditions. Whether it's for street lamps, garden lights, or decorative outdoor lighting, cast aluminum alloys provide durability and longevity, making them a popular choice for manufacturers in the lighting industry.
Outdoor Lighting Fixtures
Cast aluminum alloys are also widely used in the manufacturing of outdoor lighting fixtures. The lightweight nature of these alloys makes them easy to handle during installation, while their excellent thermal conductivity ensures efficient heat dissipation, extending the lifespan of the fixtures. Additionally, the corrosion resistance of these alloys makes them suitable for outdoor use in various weather conditions.
Gas Appliance Parts
Gas appliance parts such as burners and valves often utilize cast aluminum alloys due to their ability to withstand high temperatures and resist corrosion from gas exposure. The lightweight nature of these alloys also contributes to the overall efficiency and ease of handling during production and installation processes.
Furthermore, the cast aluminum alloys used in gas appliance parts offer excellent thermal conductivity, allowing for efficient heat transfer and distribution. This ensures that the burners and valves can operate at optimal temperatures, maximizing their performance and longevity. Additionally, the versatility of cast aluminum alloys allows for intricate designs and shapes to be easily achieved, providing manufacturers with greater flexibility in creating innovative and functional gas appliance parts.
Choosing the Best Casting Aluminum Alloy
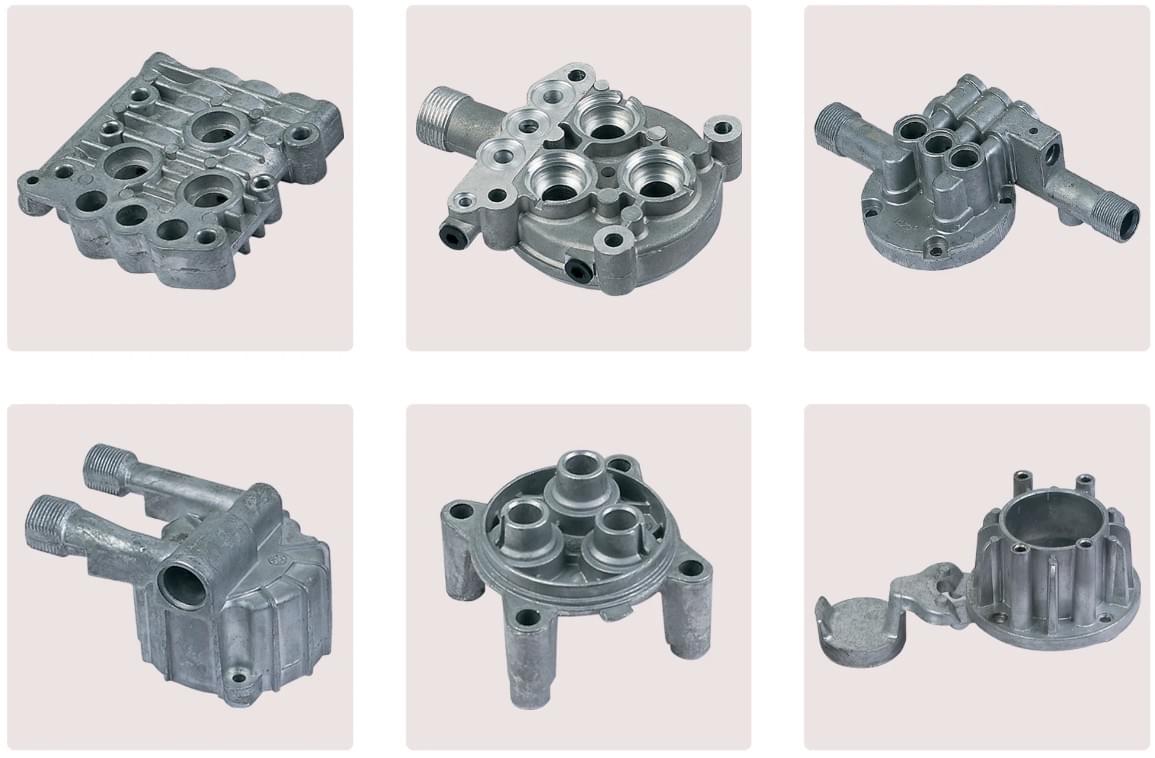
When considering the best casting aluminum alloy for your project, there are several factors to take into account. These include the specific application of the part, the required mechanical properties, and the desired surface finish. Understanding these factors will help you narrow down your options and choose the most suitable alloy for your needs.
Smart Part Engineering by Buttler is a game-changer in the industry, offering innovative tooling designs that are engineered for cost-effective manufacturing. Their expertise allows them to maximize performance and casting quality while minimizing the need for secondary operations. By taking advantage of their Engineering Design Review Process, you can optimize your new and existing parts at no cost to you, ensuring that you get the best casting aluminum alloy for your project.
Die Casting Aluminum Selection Guide
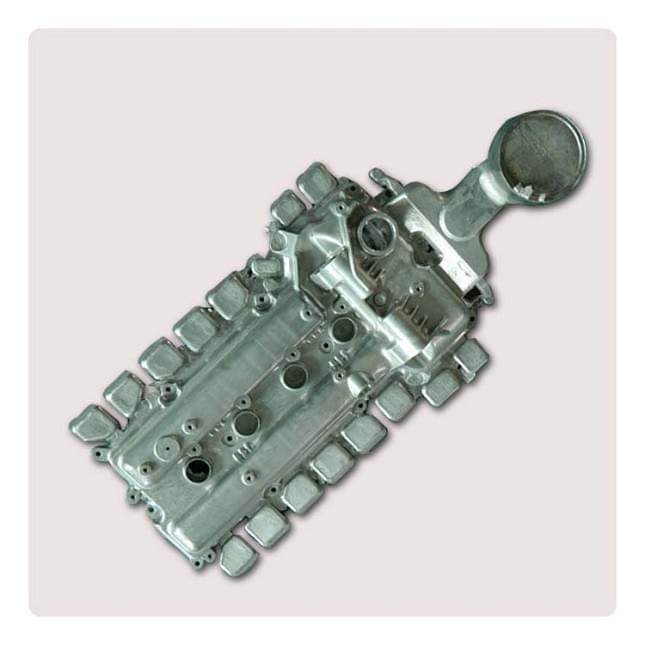
Understanding the Die Casting Process
Die casting is a manufacturing process that involves forcing molten metal into a mold cavity under high pressure. This results in precision parts with smooth surfaces and tight tolerances. For aluminum casting alloys, the die casting process is ideal for creating complex shapes with excellent dimensional accuracy and stability.
Ningbo Buttler Precision Machinery Co., Ltd. Expertise
Ningbo Buttler Precision Machinery Co., Ltd. specializes in die-casting molds and aluminum castings, offering expertise in processing, surface treatment, assembly, and packaging. Their Smart Part Engineering approach ensures better part designs, maximizing performance and quality while minimizing the need for secondary operations.
With a deep understanding of the die casting process and a commitment to innovative tooling designs, Ningbo Buttler Precision Machinery Co., Ltd. is well-equipped to provide cost-effective manufacturing solutions for aluminum casting alloys.
What alloys are in cast aluminum?
What are the cast aluminium alloys? What is the best casting aluminum alloy? These questions can be answered by leveraging the expertise of companies like Ningbo Buttler Precision Machinery Co., Ltd., who can guide you in choosing the best casting aluminum alloy for your specific application needs.
By understanding the die casting process and working with experts like Ningbo Buttler Precision Machinery Co., Ltd., you can make informed decisions when selecting from the cast aluminum alloys list to ensure optimal performance and quality for your projects.
Is 6061 a cast aluminum?
Yes, 6061 is indeed one of the commonly used cast aluminum alloys due to its excellent mechanical properties and weldability. Understanding how this alloy fits into your specific die casting needs requires expertise that companies like Ningbo Buttler Precision Machinery Co., Ltd. can provide.
Die Casting Aluminum Selection Guide - With expert guidance from companies like Ningbo Buttler Precision Machinery Co., Ltd., you can confidently navigate through the various options within the cast aluminum alloys list to choose the best alloy for your specific project requirements.
Conclusion
When it comes to making informed decisions with aluminum casting alloys, understanding the cast aluminum alloys list is crucial. Knowing what alloys are in cast aluminum will help you find the best alloy for your project. With options like 6061 aluminum alloy, it's important to consider the best casting aluminum alloy for your specific needs. The future of die casting aluminum selection looks promising, especially with resources like the Die Casting Aluminum Selection Guide and expert companies like Ningbo Buttler Precision Machinery Co., Ltd.
Making Informed Decisions with Aluminum Casting Alloys
Understanding the different types of cast aluminium alloys is essential for making informed decisions when choosing the right one for your project. By familiarizing yourself with what is available in the cast aluminum alloys list, you can ensure that you select an alloy that meets your specific requirements. With options ranging from 6061 to 380 aluminum alloy, it's important to carefully consider which one will best suit your needs.
Finding the Best Alloy for Your Project
With a variety of cast aluminium alloys to choose from, finding the best alloy for your project may seem daunting at first. However, by carefully evaluating factors such as lightweight and durable properties, corrosion resistance, and thermal conductivity, you can narrow down your options to select the most suitable casting aluminum alloy for your application. Consulting resources like Smart Part Engineering by Buttler can also provide valuable insights into optimizing part designs.
The Future of Die Casting Aluminum Selection
As technology continues to advance, so does die casting aluminum selection processes and techniques. Companies like Ningbo Buttler Precision Machinery Co., Ltd., with their expertise in die-casting molds and processing, are at the forefront of this evolution. With innovative tooling designs engineered for cost-effective manufacturing and optimized part performance, the future looks bright for die casting aluminum selection.