Introduction
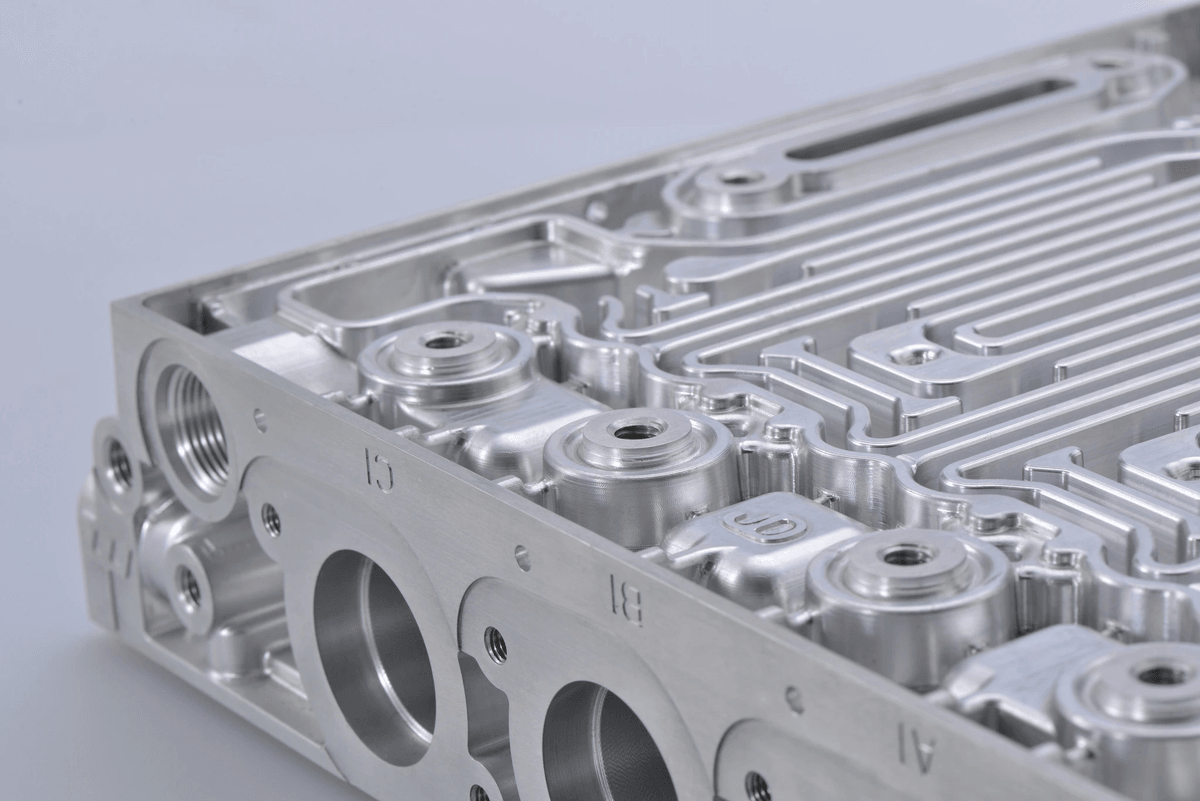
The automotive metal die-casting industry plays a crucial role in the production of high-quality vehicle components. With the increasing demand for automotive die-casting components, manufacturers focus on innovation and advanced technology to meet the industry's requirements. Die casting has become essential in the automotive industry, providing durable and complex parts for various applications.
Overview of
the Automotive Metal Die Casting Industry
The automotive metal die-casting industry is witnessing a significant shift toward producing aluminum structural components for electric vehicles. This trend is driven by the growing market for lightweight and energy-efficient automotive parts, leading to a surge in demand for die-cast aluminum components.
Increasing Demand for Automotive Die Casting Components
As the automotive industry continues to evolve, there is a rising demand for innovative die-casting technology to produce high-quality, precision automobile parts. The increasing use of aluminum structural components in electric vehicles has fueled the demand for advanced die-casting processes and materials.
The demand for automotive die-casting components is also driven by the need for lightweight yet durable parts in traditional internal combustion engine vehicles. With a focus on improving fuel efficiency and reducing emissions, automakers are turning to die-casting technology to create components that can withstand the rigors of everyday use while still being lightweight. This shift towards lighter materials has opened up new opportunities for die-casting manufacturers to showcase their expertise in producing high-quality parts that meet the stringent requirements of modern vehicles.
Role of Die Casting in Automotive Industry
Die casting is a critical technology driving the evolution of automobile manufacturing. By offering efficient and cost-effective production of complex parts, die casting significantly contributes to the automotive industry's progress.
Die-cast components play a vital role in enhancing various aspects of vehicle performance, including:
- Weight reduction: Die casting enables the creation of lightweight components, improving fuel efficiency and overall vehicle performance.
- Complex part production: The process allows for manufacturing intricate and detailed parts that would be challenging to produce using other methods.
- Cost-effectiveness: Die casting often offers a more economical solution compared to traditional manufacturing techniques, leading to overall cost savings.
Die casting is a cornerstone of modern automotive manufacturing. Its ability to produce high-quality, complex parts efficiently and cost-effectively makes it an indispensable technology for the automotive industry's continued advancement.
Automotive Die Casting Industry Trends
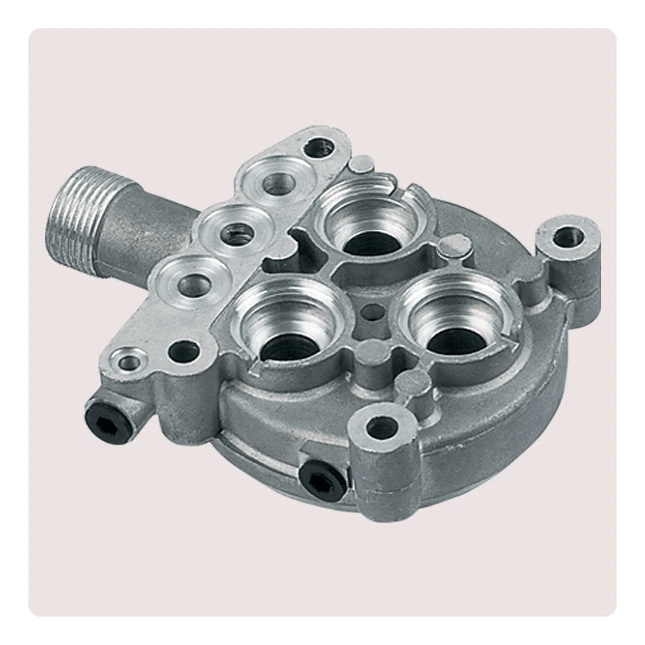
As the automotive metal die-casting industry continues to evolve, there is a growing market for aluminum structural components for electric vehicles. The shift towards electric mobility has increased demand for lightweight and durable parts, making aluminum die casting an attractive option for manufacturers looking to meet these requirements. With its excellent strength-to-weight ratio, aluminum is well-suited for structural components in electric vehicles, driving the trend towards greater use of this material in die casting.
Advancements in die-casting technology for automotive parts have also been a key trend in the industry. Manufacturers are constantly innovating to improve the efficiency and precision of die-casting processes, producing higher quality and more complex automotive components through this method. These advancements have enabled the production of intricate parts with tight tolerances, contributing to modern vehicles' overall performance and safety.
Furthermore, emerging trends in casting parts in automobiles are shaping the future of automotive die casting. From lightweight initiatives to sustainability efforts, manufacturers are exploring new materials and processes to enhance automotive components' performance and environmental impact. This includes adopting innovative alloys, improved surface treatments, and advanced simulation tools to optimize part designs and manufacturing processes.
With these trends driving innovation and growth in the automotive die-casting industry, manufacturers must stay ahead by embracing new technologies and materials while addressing environmental concerns and quality standards. As Ningbo Buttler Precision Machinery Co., Ltd. continues to lead with smart part engineering solutions and a focus on sustainable practices, they are well-positioned to capitalize on these emerging trends and provide cutting-edge solutions for automotive parts production.
Key Players in the Automotive Die Casting Industry
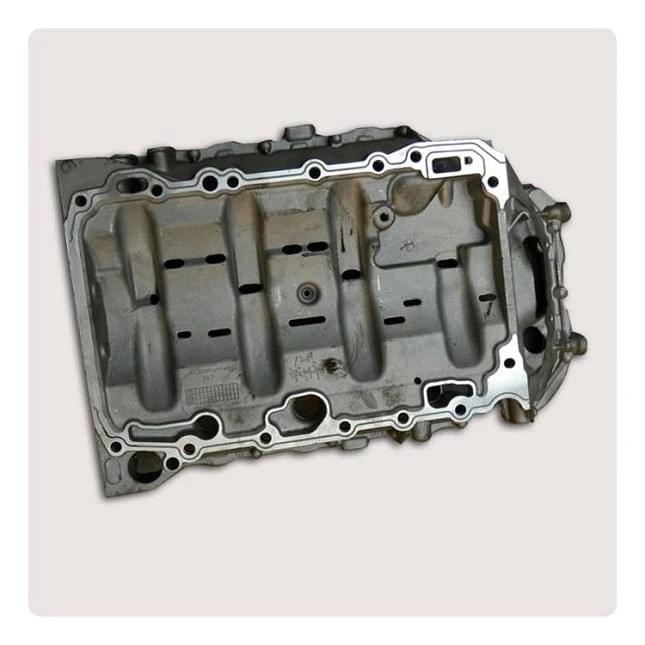
Ningbo Buttler Precision Machinery Co., Ltd. is a leading player in the automotive metal die-casting industry. It specializes in high-quality die-casting molds, aluminum and zinc castings, processing, surface treatment, assembly, and packaging. With its expertise in smart part engineering, it focuses on creating better part designs that maximize performance and casting quality while minimizing the need for secondary operations.
Introduction to Ningbo Buttler Precision Machinery Co., Ltd.
Ningbo Buttler Precision Machinery Co., Ltd. is a leading provider of automotive die-casting solutions, specializing in die-casting molds and aluminum and zinc castings. Their commitment to innovation and excellence has solidified their position as a trusted partner for automotive parts manufacturers worldwide.
Ningbo Buttler offers a comprehensive range of services, including:
- Precision die-casting mold design and manufacturing
- High-quality aluminum and zinc castings
- Advanced engineering and technical support
With a strong focus on customer satisfaction, Ningbo Buttler delivers exceptional products and services that meet the stringent demands of the automotive industry. Their dedication to quality, efficiency, and continuous improvement ensures they remain at the forefront of automotive die-casting technology.
Ningbo Buttler Precision Machinery Co., Ltd. is your ideal partner for all your automotive die-casting needs.
Smart Part Engineering for Better Part Designs
At Ningbo Buttler Precision Machinery Co., Ltd., smart part engineering is a priority. Their team of experts focuses on creating innovative tooling designs engineered for cost-effective manufacturing while maximizing performance and casting quality. By optimizing new and existing parts through their Engineering Design Review Process, they ensure superior results at no additional cost to their clients.
Ningbo Buttler Precision Machinery Co., Ltd. also offers comprehensive design and engineering services to help clients bring their part designs to life. Their team works closely with clients to understand their needs and challenges, providing tailored solutions that meet or exceed expectations. Whether creating prototypes, optimizing existing designs, or developing new tooling concepts, Ningbo Buttler Precision Machinery Co., Ltd. has the expertise and resources to deliver exceptional results.
Services Offered by Ningbo Buttler Precision Machinery Co., Ltd.
Ningbo Buttler Precision Machinery Co., Ltd. offers a comprehensive range of services, including die-casting molds, aluminum and zinc castings, processing, surface treatment, assembly, and packaging. Their dedication to providing end-to-end solutions sets them apart as a key player in the automotive metal die-casting industry.
Ningbo Buttler Precision Machinery Co., Ltd. also prides itself on its ability to customize solutions to meet each client's specific needs. Whether creating unique die-casting molds or providing specialized surface treatments, their team of experts is dedicated to delivering high-quality, tailor-made products. This level of customization sets them apart from their competitors and ensures that their clients receive the components they require for their automotive applications.
Market Opportunities in Automotive Parts Die Casting
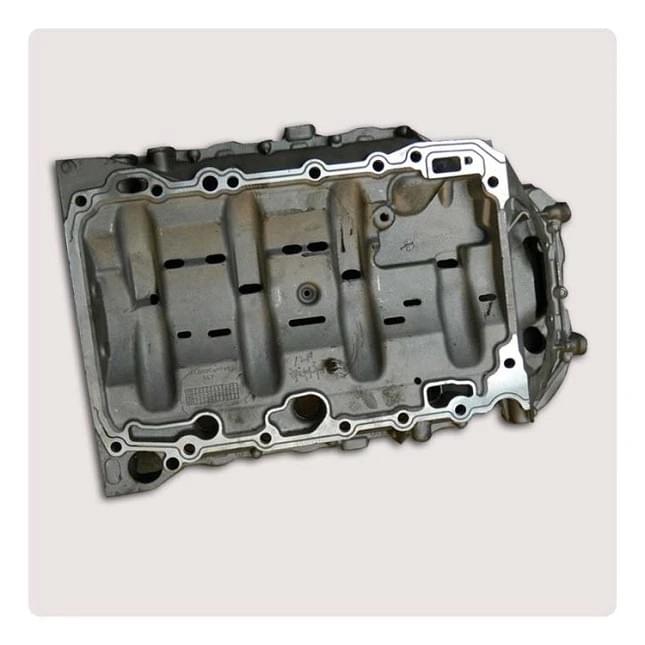
The automotive metal die-casting industry presents lucrative opportunities for manufacturers in various product segments. One such area is the outdoor lamp series, where die-cast components are essential for durability and aesthetics. With the increasing demand for energy-efficient lighting solutions, there is a growing market for die-cast parts that offer superior performance and longevity in outdoor environments.
Opportunities in
the Outdoor Lamp Series
Ningbo Buttler Precision Machinery Co., Ltd. specializes in providing high-quality die-cast components for outdoor lighting fixtures. Their expertise in smart part engineering ensures the parts are designed to withstand harsh weather conditions while maintaining an appealing appearance. This makes them a preferred partner for manufacturers looking to capitalize on the opportunities within the outdoor lamp series segment of the automotive parts die-casting market.
Ningbo Buttler offers several key advantages to its partners:
- Expertise in smart part engineering: Ensuring components are durable and aesthetically pleasing.
- Focus on outdoor lighting fixtures: Deep understanding of this market's specific challenges and requirements.
- Commitment to sustainability: Producing energy-efficient components to meet growing consumer demand.
By partnering with Ningbo Buttler, manufacturers can gain a competitive edge in the outdoor lighting market by offering innovative, durable, and eco-friendly products.
Ningbo Buttler is committed to supporting its partners in achieving their business goals and contributing to a more sustainable future.
Challenges in the Automotive Metal Die Casting Industry
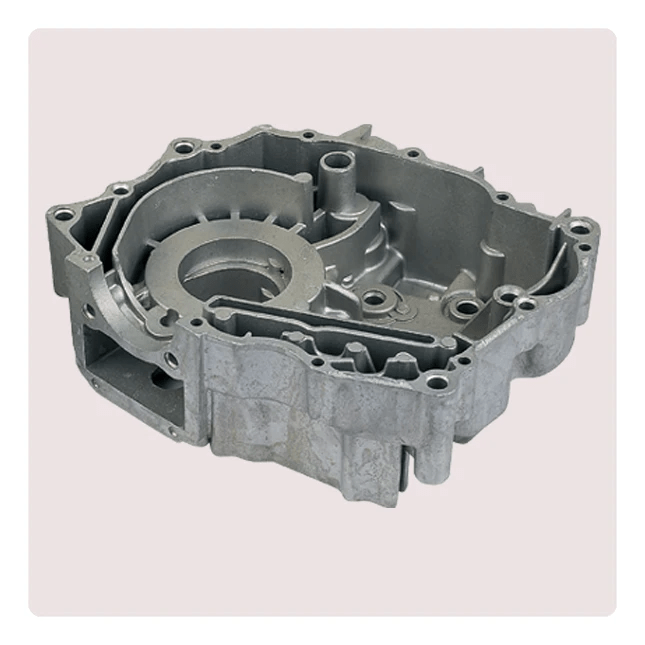
Addressing Environmental Concerns in
Die-Casting
The automotive metal die-casting industry faces the challenge of addressing environmental concerns related to using materials and energy in manufacturing. With a growing emphasis on sustainability, die-casting companies must explore eco-friendly practices and materials to minimize their environmental impact.
Furthermore, die-casting companies can also invest in advanced technology and equipment to reduce energy consumption and emissions during manufacturing. Implementing automation and robotics can help optimize energy usage and minimize waste, contributing to a more sustainable operation. Additionally, exploring alternative energy sources such as solar or wind power can reduce the environmental impact of die-casting operations.
Meeting Quality Standards in Automotive Parts
Ensuring high-quality standards for automotive parts die casting is crucial to meet modern vehicles' performance and safety requirements. Manufacturers must invest in advanced technologies and stringent quality control measures to consistently produce components that meet or exceed industry standards.
Automotive parts die-casting manufacturers should also focus on process optimization and waste reduction to achieve cost-effective manufacturing and minimize secondary operations. By streamlining production processes and implementing lean manufacturing principles, companies can reduce material waste and energy consumption, ultimately lowering production costs. Additionally, investing in automation and robotics can help minimize the need for secondary operations, such as machining or finishing, further reducing overall manufacturing expenses.
Cost-Effective Manufacturing and Minimizing Secondary Operations
Cost-effective manufacturing and minimizing secondary operations are key challenges the automotive die-casting industry faces. Companies need to focus on optimizing production processes, reducing waste, and implementing efficient machining techniques to minimize the need for additional finishing operations, thereby lowering overall production costs.
To address the challenge of optimizing production processes, automotive die-casting companies can invest in advanced technologies such as real-time monitoring systems and predictive maintenance tools. These innovations can help identify potential issues before they escalate, allowing for proactive adjustments to the production line. By leveraging these technologies, companies can minimize downtime, improve overall equipment effectiveness, and reduce manufacturing costs.
Future Outlook for the Automotive Metal Die Casting Industry
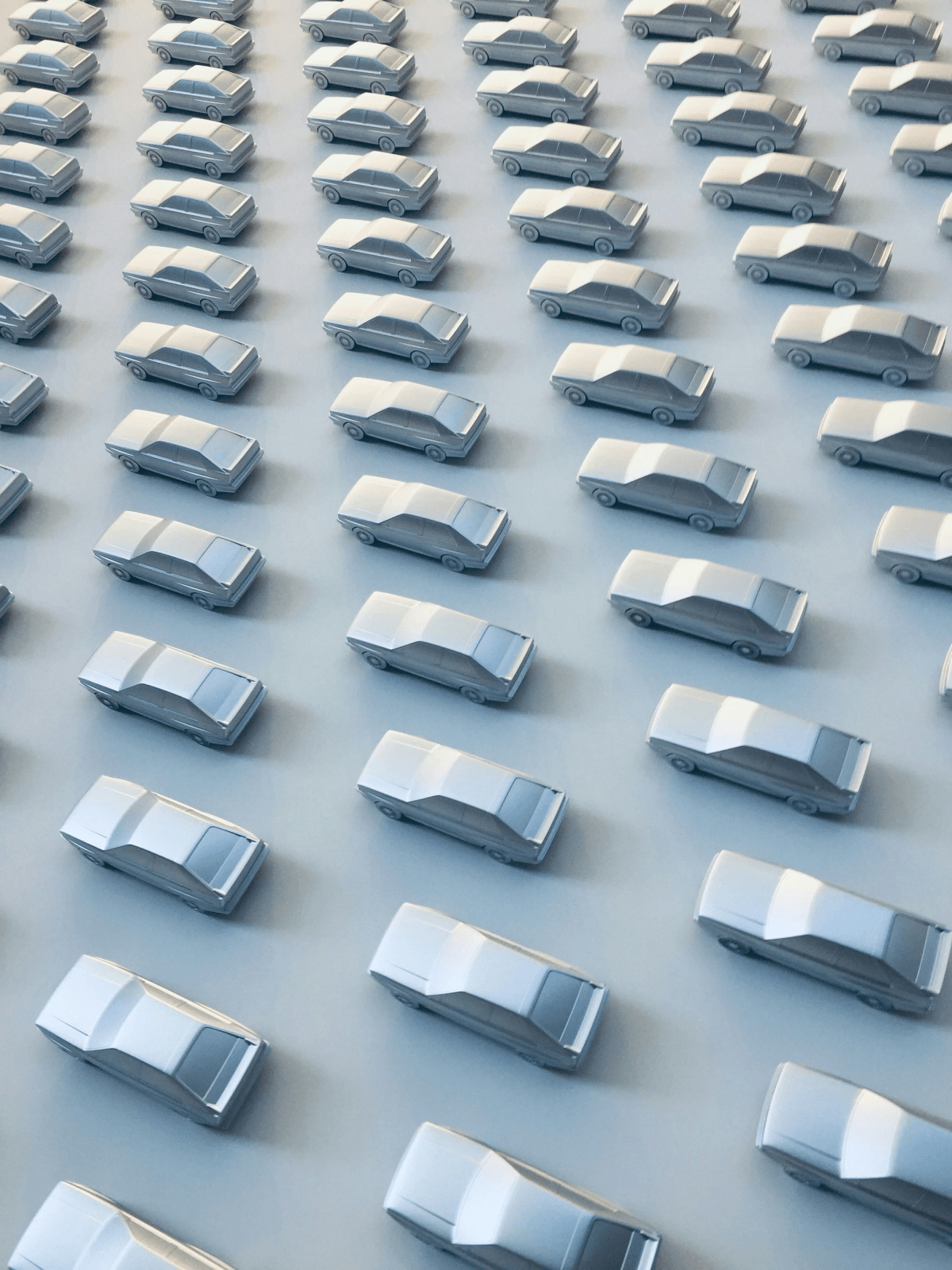
The future of the automotive metal die-casting industry looks promising, with the increasing demand for lightweight and durable automotive parts. The industry is expected to witness significant growth, driven by the rising adoption of electric vehicles and advancements in die-casting technology for automotive components.
Key Considerations for Automotive Parts Manufacturers
Automotive parts manufacturers must focus on leveraging aluminum structural components for electric vehicles to meet the growing market demand. They should also prioritize smart part engineering for better design, ensuring cost-effective manufacturing and high-quality casting without extensive secondary operations.
Furthermore, automotive parts manufacturers should invest in advanced simulation and modeling technologies to optimize the design and performance of aluminum structural components. This will enable them to reduce material waste, improve energy efficiency, and enhance overall sustainability in the production process. By embracing innovative engineering solutions, manufacturers can stay ahead of the competition and meet the evolving needs of electric vehicle manufacturers.
Importance of Innovation and Sustainable Practices in Die Casting Industry
Innovation and sustainable practices are crucial for the die-casting industry to thrive in the automotive sector. Companies like Ningbo Buttler Precision Machinery Co., Ltd. are leading the way with their expertise in die-casting molds, aluminum and zinc castings, and innovative tooling designs engineered for cost-effective manufacturing.
Future Outlook for
the Automotive Metal Die Casting Industry
The future of the automotive metal die-casting industry looks promising, with the increasing demand for lightweight and durable automotive parts. The industry is expected to witness significant growth, driven by the rising adoption of electric vehicles and advancements in die-casting technology for automotive components.
The automotive industry's increasing focus on sustainability and environmental consciousness is also expected to drive the demand for metal die casting. As automakers seek to reduce their carbon footprint, they turn to lightweight materials such as aluminum and magnesium, which can be efficiently produced through die-casting. This shift towards eco-friendly manufacturing processes presents a significant opportunity for metal die-casting manufacturers to capitalize on.
Key Considerations for Automotive Parts Manufacturers
Automotive parts manufacturers must focus on leveraging aluminum structural components for electric vehicles to meet the growing market demand. They should also prioritize smart part engineering for better design, ensuring cost-effective manufacturing and high-quality casting without extensive secondary operations.
Importance of Innovation and Sustainable Practices in Die Casting Industry
Innovation and sustainable practices are crucial for the die-casting industry to thrive in the automotive sector. Companies like Ningbo Buttler Precision Machinery Co., Ltd. are leading the way with their expertise in die-casting molds, aluminum and zinc castings, and innovative tooling designs engineered for cost-effective manufacturing.
In addition to their expertise in traditional die-casting methods, companies like Ningbo Buttler Precision Machinery Co., Ltd. also embrace innovative technologies such as 3D printing and digital simulation for mold design and production. Incorporating these advanced techniques can improve efficiency, reduce material waste, and minimize energy consumption, contributing to a more sustainable manufacturing process.