Introduction
When it comes to die casting, understanding the basics of die cast aluminium is crucial for successful manufacturing. Die casting involves forcing molten metal into a die or mold cavity under high pressure. This process is especially advantageous when working with aluminum, as it offers excellent thermal conductivity and can be easily cast into complex shapes. Choosing the right material for die casting is essential, and aluminum alloy material provides a lightweight yet durable solution for a wide range of applications.
Understanding the Basics of Die Cast Aluminium
Die cast aluminium refers to the process of injecting molten aluminum into a steel mold to create complex shapes with high precision and accuracy. This method allows for the production of intricate parts that require minimal machining or finishing, making it a cost-effective solution for many industries.
Advantages of Aluminum Die Casting
Aluminum die casting offers numerous advantages, including lightweight yet strong components, excellent corrosion resistance, and high dimensional stability. Additionally, aluminum's ability to withstand high operating temperatures makes it an ideal choice for various applications in automotive, aerospace, and consumer electronics industries.
The Importance of Choosing the Right Material for Die Casting
Selecting the right material for die casting is crucial to ensure optimal performance and durability of the finished product. Aluminum alloy materials provide superior strength-to-weight ratio, excellent machinability, and exceptional thermal conductivity, making them an ideal choice for a wide range of die casting applications.
Selecting the Right Die Casting Process
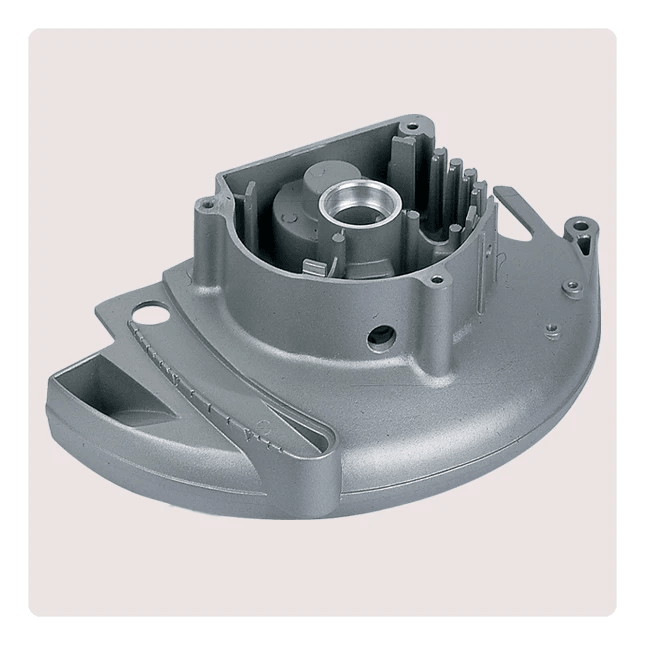
When it comes to die casting, choosing the right process is crucial for the success of your project. High pressure die casting and low pressure die casting are two common methods used in the industry. High pressure die casting involves injecting molten metal into a steel mold at high pressure, resulting in fast cycle times and high production rates. Low pressure die casting, on the other hand, utilizes low air pressure to fill the mold cavity with molten metal, making it ideal for large and complex parts with thin walls.
High Pressure Die Casting vs. Low Pressure Die Casting
High pressure die casting offers excellent dimensional accuracy and smooth surface finishes, making it suitable for a wide range of applications. On the other hand, low pressure die casting is known for its ability to produce parts with minimal porosity and excellent mechanical properties. When deciding between these two processes, it's important to consider factors such as part complexity, production volume, and desired properties of the final product.
Gravity Die Casting vs. Vacuum Die Casting
Gravity die casting relies on gravity to fill the mold cavity with molten metal, resulting in high-quality parts with superior mechanical properties. Vacuum die casting, on the other hand, uses a vacuum to remove air from the mold cavity before filling it with molten metal, ensuring minimal porosity and excellent surface finishes. Both processes offer unique advantages depending on the specific requirements of your project.
Choosing the Most Suitable Process for Your Project
Selecting the most suitable die casting process for your project requires careful consideration of various factors such as part design, material selection, production volume, and cost constraints. It's essential to work with a trusted partner like Ningbo Buttler Precision Machinery Co., Ltd., who specializes in providing comprehensive die-casting solutions from mold design to surface treatment and assembly. By leveraging their expertise in smart part engineering and innovative tooling designs engineered for cost-effective manufacturing, you can ensure optimal performance while minimizing secondary operations.
Design Considerations for Die Casting
Importance of Smart Part Engineering
When it comes to die casting, smart part engineering is crucial for achieving the best possible designs. By utilizing innovative tooling designs from Ningbo Buttler Precision Machinery Co., Ltd., you can ensure that your parts are engineered for cost-effective manufacturing, maximizing performance and casting quality while minimizing the need for secondary operations.
Designing for Cost-Effective Manufacturing
Designing for cost-effective manufacturing is essential in die casting to ensure efficient production processes and minimize unnecessary expenses. With the expertise of Ningbo Buttler Precision Machinery Co., Ltd., you can optimize your part designs through their Engineering Design Review Process, allowing you to achieve cost-effective manufacturing without compromising on quality.
Maximizing Performance and Casting Quality through Innovative Tooling Designs
Innovative tooling designs play a significant role in maximizing performance and casting quality in die casting operations. By leveraging the expertise of Ningbo Buttler Precision Machinery Co., Ltd., you can benefit from their advanced tooling designs that are engineered to enhance performance and ensure high-quality castings, ultimately leading to superior end products.
Material Selection for Aluminum Die Casting
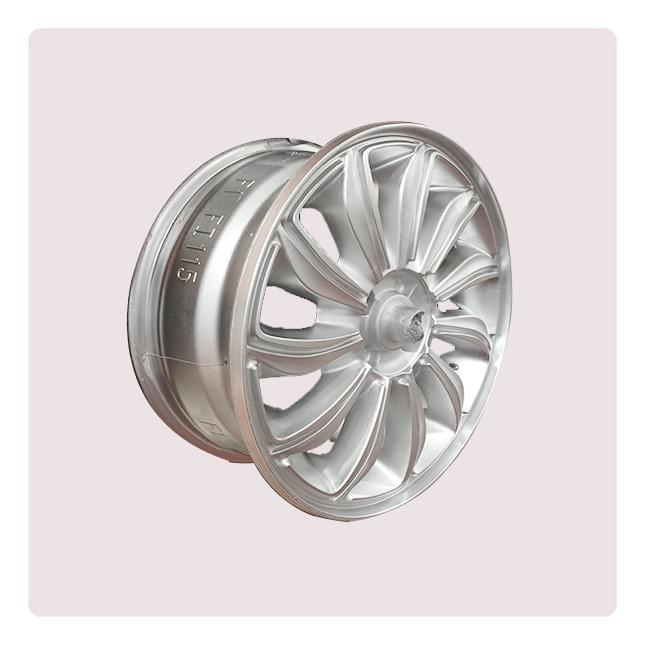
Exploring Different Aluminum Alloy Materials
When it comes to die casting, the material used plays a crucial role in the final product's quality and performance. Aluminum alloys are a popular choice due to their lightweight yet durable properties, making them ideal for a wide range of applications. Some common aluminum alloy materials include A380, A383, and ADC12, each with its own unique set of characteristics and benefits for die casting.
Comparing Aluminum Alloy to Other Materials
In comparison to other materials such as steel or iron, aluminum alloys offer distinct advantages in terms of weight reduction, corrosion resistance, and thermal conductivity. These properties make aluminum alloys an attractive choice for industries seeking cost-effective solutions without compromising on strength and durability.
Understanding the Properties of Different Aluminum Alloys
Understanding the specific properties of different aluminum alloys is essential for selecting the most suitable material for your die casting project. For example, A380 offers excellent fluidity and pressure tightness, while ADC12 provides superior machinability and corrosion resistance. By carefully evaluating these properties, you can make an informed decision that aligns with your project requirements.
Quality Control in Die Casting
When it comes to die cast aluminium, ensuring proper surface treatment and finishing is crucial for achieving the desired aesthetics and functionality of the final product. The right surface treatment can enhance the corrosion resistance, durability, and overall appearance of the die cast parts, making it an essential aspect of quality control in die casting.
Ensuring Surface Treatment and Finishing
Proper surface treatment involves techniques such as shot blasting, powder coating, anodizing, or painting to protect the die cast aluminium from environmental factors and improve its visual appeal. By paying close attention to surface treatment and finishing, manufacturers can ensure that their die cast parts meet industry standards and customer expectations for quality and performance.
Importance of Assembly and Packaging in Quality Assurance
In addition to surface treatment, assembly and packaging play a crucial role in maintaining the integrity of die cast aluminium parts. Proper assembly ensures that all components fit together seamlessly, while effective packaging protects the finished products during transit and storage. Both aspects are vital for delivering high-quality products to customers.
Utilizing Ningbo Buttler Precision Machinery Co., Ltd. for Quality Die Casting
When it comes to quality die casting solutions, Ningbo Buttler Precision Machinery Co., Ltd. stands out as a reliable partner with expertise in die-casting molds, aluminum and zinc castings, processing, surface treatment, assembly, and packaging. Their commitment to smart part engineering ensures that every aspect of the manufacturing process is optimized for quality and efficiency.
Optimizing Production Efficiency
Taking Advantage of Engineering Design Review Process
When it comes to die casting, maximizing production efficiency starts with the engineering design review process. By partnering with Ningbo Buttler Precision Machinery Co., Ltd., you can take advantage of their expertise in providing innovative tooling designs engineered for cost-effective manufacturing. This process helps to optimize new and existing parts, ensuring that they are manufactured efficiently and effectively.
Maximizing Performance while Minimizing Secondary Operations
One key aspect of optimizing production efficiency in die casting is to maximize performance while minimizing the need for secondary operations. With the right die cast die and smart part engineering, it's possible to achieve high-quality castings without the need for extensive secondary processes. This not only saves time but also reduces costs, making the entire production process more efficient.
Cost-Effective Manufacturing with Smart Part Engineering
Smart part engineering is essential for achieving cost-effective manufacturing in die casting. By leveraging innovative tooling designs and smart part engineering from Ningbo Buttler Precision Machinery Co., Ltd., manufacturers can streamline their production processes and achieve significant cost savings. This approach ensures that every part is designed for efficient manufacturing, resulting in high-quality castings at a lower cost.
Die Casting Troubleshooting and Maintenance
When it comes to die casting, common issues such as air entrapment, shrinkage porosity, and cold shuts can arise. These issues can be addressed by adjusting the die cast die temperature, pressure, and injection speed. Preventative maintenance for die casting equipment is crucial to ensure longevity and reliability in operations. Regular cleaning, lubrication, and inspection of the die for casting can help prevent downtime and costly repairs. By following these maintenance practices, you can ensure that your alum cast operations run smoothly and efficiently.
Common Issues in Die Casting and How to Address Them
Common issues in die casting include air entrapment, shrinkage porosity, and cold shuts. To address air entrapment, it's important to optimize the venting system of the die cast die to allow trapped air to escape during the casting process. Shrinkage porosity can be minimized by adjusting the cooling rate of the aluminum alloy material to reduce solidification shrinkage. Cold shuts can be addressed by optimizing the gate system design to ensure proper filling of the mold cavity.
Preventative Maintenance for Die Casting Equipment
Preventative maintenance for die casting equipment involves regular cleaning, lubrication, and inspection of critical components such as the injection system, plunger rods, and ejector pins. It's also important to monitor the condition of the material aluminium alloy used in the process to ensure consistent quality in castings. By implementing a proactive maintenance schedule, you can prevent unexpected breakdowns and prolong the lifespan of your equipment.
Ensuring Longevity and Reliability in Die Casting Operations
To ensure longevity and reliability in die casting operations, it's essential to partner with a reputable company like Ningbo Buttler Precision Machinery Co., Ltd. Their expertise in die-casting molds, aluminum and zinc castings processing, surface treatment, assembly, and packaging ensures that your operations run smoothly from start to finish. By leveraging their smart part engineering solutions engineered for cost-effective manufacturing, you can maximize performance while minimizing secondary operations.
Future Trends in Die Casting
Innovations in Die Casting Technology
As the demand for lightweight, durable components continues to grow, die casting technology is evolving to meet these needs. Innovations such as advanced simulation software and real-time monitoring systems are revolutionizing the die casting process, allowing for more precise and efficient production of die cast aluminium parts. These technological advancements are paving the way for faster production cycles and higher quality products, positioning die casting as a leading manufacturing solution in various industries.
Sustainable Practices in Die Casting
With an increasing focus on sustainability, the die casting industry is embracing environmentally friendly practices to minimize waste and energy consumption. From implementing closed-loop systems to recycling scrap materials, sustainable initiatives are becoming integral to die casting operations. Companies like Ningbo Buttler Precision Machinery Co., Ltd. are at the forefront of sustainable practices, offering eco-friendly solutions for die cast aluminium production that prioritize efficiency and environmental responsibility.
The Evolution of Die Casting in Manufacturing Industries
As technology continues to advance, die casting is expected to play a pivotal role in shaping the future of manufacturing industries. The versatility and cost-effectiveness of die cast aluminium make it a preferred choice for a wide range of applications, from automotive components to consumer electronics. With ongoing advancements in material science and process optimization, die casting is poised to remain a key player in the ever-changing landscape of manufacturing.
Conclusion
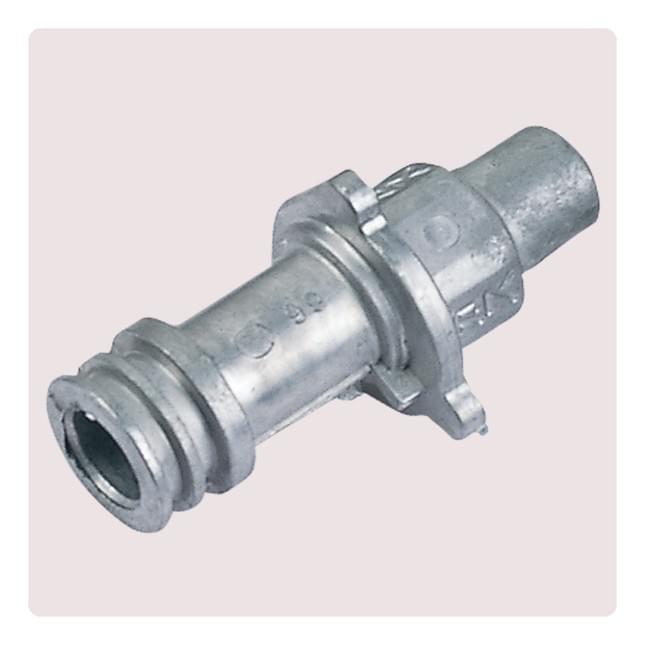
In conclusion, die cast aluminium is a versatile and efficient material for die casting projects, offering numerous advantages in terms of strength, durability, and cost-effectiveness. Leveraging Ningbo Buttler Precision Machinery Co., Ltd. for die casting solutions ensures top-quality production, from smart part engineering to surface treatment and finishing. As the future of die casting evolves towards sustainability and innovation, it's crucial to stay ahead of the curve and embrace the latest advancements in technology and practices.
Ensuring Quality and Efficiency in Aluminum Die Casting
When it comes to ensuring quality and efficiency in aluminum die casting, choosing the right material is crucial for successful outcomes. With its superior properties, aluminum alloy material is a popular choice for die casting applications due to its lightweight nature and excellent thermal conductivity. By selecting the most suitable alum cast for your project, you can optimize production efficiency while maintaining high-quality standards throughout the manufacturing process.
Leveraging Ningbo Buttler Precision Machinery Co., Ltd. for Die Casting Solutions
Ningbo Buttler Precision Machinery Co., Ltd. offers comprehensive die-casting solutions that encompass every aspect of the process, from mold design to assembly and packaging. Their expertise in smart part engineering ensures that your parts are designed for cost-effective manufacturing without compromising on performance or quality. By leveraging their services, you can streamline your production processes and achieve exceptional results with minimal need for secondary operations.
The Future of Die Casting: Innovations and Sustainability
As the future of die casting continues to evolve, innovations in technology are shaping the industry towards more sustainable practices. With a focus on environmental consciousness and resource efficiency, manufacturers are embracing sustainable materials and processes to reduce their carbon footprint while maintaining high standards of quality. By staying abreast of these developments and incorporating them into your die casting operations, you can position yourself at the forefront of industry trends while contributing to a greener future.
Remember that excellence in aluminum die casting lies not only in choosing the right material but also in partnering with experts who understand every facet of the process – from design considerations to quality control measures – ensuring that your products meet or exceed industry standards consistently.